Lagging To Leading—Improving Safety With A Near-Miss Standard
Collecting near-miss reports is an essential part of a safety management system (SMS).
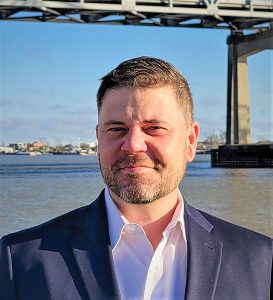
A near-miss is an unplanned event that did not result in injury or damage—but had the potential to do so. Establishing a system for reporting these leading indicators allows our vessel crews, tankermen and other boots-on-deck team members to share safety concerns with shoreside management before the concern causes an injury, environmental incident, equipment damage or even a fatality. The benefit of collection seems obvious, but creating and managing a successful program that transforms reports into positive policy changes is not such an easy task.
Without leading-indicator collection, we rely on incident investigations and the lagging indicators they produce to reveal workplace hazards and weaknesses in our SMS. While it is imperative that we learn from our mistakes, using lagging indicators to drive policy improvement comes at the expense of the injury or equipment damage that led to the investigation.
Currently, many voluntary SMS standards, company-specific safety and environmental programs, customer vetting programs and industry best practices recommend or require leading-indicator collection and an accompanying corrective action process, and these collections allow a company to benchmark its own performance. However, without an accepted standard, comparison across the industry based on leading indicators remains out of reach.
While there are standardized collections of incident data, including those maintained by the U.S. Coast Guard, the National Transportation Safety Board and the American Waterway Operators (AWO) Safety Statistics Reporting Program, there is not a standard leading-indicator collection system currently in use by a majority of the maritime industry.
This is not to say that there are no references. Resources that discuss leading-indicator collection include (but are not limited to) publications by the International Maritime Organization (IMO), International Organization for Standardization (ISO), National Safety Council (NSC), Occupational Safety and Health Administration (OSHA) and American Society for Testing and Materials (ASTM). There are also some vetting programs, like the Tanker Management Self-Assessment (TMSA) program developed by the Oil Companies International Marine Forum, which require near-miss collection but leave specific reporting criteria up to the individual program participant.
To provide an opportunity for industry benchmarking, there must be a practical voluntary standard that is specific enough to allow comparison and flexible enough to be used throughout our industry’s vastly diverse operations.
There are barriers to an industry collection system that must be addressed when developing a program, including identifying a collection agent. A federal agency like the Coast Guard, while well-positioned to collect information through its Marine Information for Safety and Law Enforcement (MISLE) system, could not serve as a collection agent due to its regulatory role. The Coast Guard’s duty to investigate reports of legal infractions and unseaworthy conditions would discourage industry from submitting information and lead to a watered-down system that does not capture the high-value near misses necessary to drive improvements to industry safety performance.
So, who could collect these leading indicators, and what should the standard for collection be? Here, the challenges of creating a system for the industry mirror those faced on a company level. There needs to be agreement on what information will be recorded, who will manage the data and what the product of the reports will be. Additionally, the reporting process should align with established data collection efforts to reduce the administrative burden on reporting companies.
Further, the system should facilitate comparison through rates, which can be based on common denominators that are readily available to participants, such as man-hours or transfers. The system should produce trending reports for participants and highlight lessons learned from high-value entries. And, perhaps most crucial to deployment, the system must ensure the anonymity of reporters to protect the interests of the submitting companies while still encouraging reports that include details necessary to production of benchmarking tools and lessons learned.
To address these barriers, safety leaders at organizations including AWO, the Maritime Administration, the Ship Operations Cooperative Program and many individual towing companies are working together to produce a voluntary near-miss standard that establishes the criteria to inform reports and establishes the definitions for the data fields that make up the collection form or application. This voluntary standard will ensure that the data collected is useful for comparison, a key issue impacting the utility of the near-miss data available to date.
The appetite for a leading-indicator collection system is palpable, discussed by safety professionals at every opportunity, and the tugboat, towboat and barge industry has a great record of pursuing initiatives that advance marine safety beyond contemporary regulation. A clear recent example is the towing vessel inspection regime at 46 CFR Subchapter M, fully implemented in July, which was built on the industry-developed framework of the AWO Responsible Carrier Program, first established in 1994.
As an industry, we are well experienced and motivated to improve safety at every opportunity, and the establishment of a voluntary near-miss standard would be a critical step forward in accelerating our progress and evolution. There are many challenges, but none are insurmountable.
Michael Breslin is Director of Safety and Sustainability for The American Waterways Operators (AWO). His focus in this role is to advance the safety culture and sustainability of the nation’s tugboat, towboat and barge industry. Breslin got his start in the marine industry in 2009 as a deckhand for Turn Services, in New Orleans. He held positions in logistics, safety, training, claims, compliance and operations prior to joining AWO in December 2021.