Supply Chain: Crisis, Solutions And Opportunities
By Grady S. Hurley
The supply chain reportedly stalled following the COVID-19 outbreak, creating shortages, price increases and frustration. The recent spotlight on supply chain logistics has focused on ports and terminals where ships were at anchorage and containers stacked high in yards. The terminal gridlock may just be a symptom of bigger problems. What is the “supply chain,” and how can the maritime industry help identify the issues and be part of the solution?
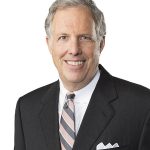
A supply chain is a system of distribution between manufacturers, suppliers, retailers and consumers. Like the game of dominoes, each segment is dependent on the other. The system challenges sourcing, scheduling and logistics to efficiently deliver goods and, by the way, is highly regulated by governmental agencies. Supply chain reliabilities require public-private collaboration to perform efficiently.
Supply chain logistics relies on intermodal transportation, including vessels, rail, trucking and air, to deliver goods that are sourced and manufactured internationally.
The significance and fragility of intermodal transportation in world trade was addressed by the U.S. Supreme Court in Norfolk So. R.R. Co. v. James N. Kirby, PTY, Ltd. (2004) and again in Kawasaki Kesen Kaisha, Ltd. v. Regal Beloit Corp. (2010). In those decisions, the Court recognized that federal laws, like the 1906 Carmack Amendment, were not aligned with the realities of modern multimodal international commerce. To foster consistency in the movement of goods internationally, the Court relied on bills of lading issued by carriers to establish applicable laws for carriage because the “intermodal transportation industry clearly has moved into a new era—the age of multimodalism door-to-door transport based on efficient use of all available modes of transportation by air, water and land.”
What factors in recent years have affected the “efficient use” of transportation for delivery? The answer is “many.”
Supply Chain Obstacles
Supply chain obstacles involving the international transportation of goods historically focused on politics, tariffs and embargoes. A pandemic was not an anticipated obstacle. COVID-19, however, affected all segments of the supply chain, from sourcing to delivery. It also exposed and accelerated long-existing weaknesses affecting our supply chain—the proverbial weak links—that had been singularly addressed.
For example, in 2016, the Federal Maritime Commission (FMC) convened industry leader teams to address supply chain reliability and resilience through “process innovation.” Following various hearings, in 2018, the FMC initiated Fact Finding 28 to address detention, demurrage and efficient commercial practices. A final report was issued in August 2019 to facilitate “fluidity and overall performance of the American freight delivery system” along with recommendations to establish a shipping advisory board.
In early 2020, COVID-19 shut down the international freight delivery system and highlighted many weaknesses. As a result of the global pandemic, manufacturers shut down production, shippers and carriers were grounded as personnel were sequestered and ships denied port access, and inventory sat at terminals along with empty containers because of labor shortages. A supply chain perfect storm occurred in late 2020 and early 2021 when U.S. administration policies and initiatives provided a relief package to U.S. citizens that stimulated consumer demand without encouraging return to work. There was still a labor shortage, which is critical to the supply chain delivery system. Further, U.S. policies tended to encourage more imports than U.S. manufacturing, which led to the present crisis of dependence on imported goods that could not then be moved to satisfy consumer demand.
In June 2021, the Biden administration initiated a task force recognizing the lingering and growing supply chain issues beyond distribution. However, at almost the same time, the administration in July issued an executive order expressing concerns about competitive pricing and declared a “failed experiment” in terminal operations, while at the same time trying to collaborate with the transportation industry in resolving supply chain issues. Government interference can be both a cause of and a solution to any crisis, and the United States has recently focused on long-term solutions as crisis management efforts have begun to move imported goods across the country.
Solutions And Opportunities
Restarting the supply chain from its sources to consumers is not and was not like opening a faucet that had been shut off. The intermodal transportation system is interdependent on many factors and must be sequentially addressed. In many cases, the infrastructure was in place but the people to move goods as demand rose were not. In other instances, the lack of infrastructure created gridlock.
Crises often present opportunities. Current supply chain solutions began by recognizing that systemic problems existed and that each port, each terminal complex and adjoining facilities may have unique issues based on many factors, including geography and infrastructure. The long-term solutions require an understanding of the interplay between manufacturing, infrastructure, intermodal transportation, labor, taxation, regulation and the need for collaboration and innovation.
In recognition of the ramifications of COVID-19 on the international and intermodal transportation systems, John Porcari was appointed as a supply chain czar in August by President Biden to help communicate, coordinate and facilitate the movement of goods from terminals to consumers. Previously, Porcari was a port director in Baltimore, Md., with practical insights into complex port operations. In October, as the holidays approached, the administration issued a fact sheet recognizing a 39 percent increase in commerce during the first quarter of 2021, while critical labor issues to move goods continued. A 24/7 terminal operations initiative was undertaken as a temporary solution where businesses and unions collaborated in moving stockpiled goods from the West Coast to meet increasing domestic demands. Ports in the Gulf of Mexico and on the East Coast offered alternatives to West Coast deliveries.
In early November, the Georgia Ports Authority reported initial success in moving cargo by setting up landlocked pop-up container yards to be connected by trucks and rail. Recognizing the value of rivers as interstate highways, the barge industry offered “float freight” opportunities to move containers on flat-deck barges in lieu of trucking. The Mississippi River, which has traditionally barged commodities from the Midwest to the Gulf of Mexico, now offers such a highway system between deep-draft container ships and lightering onto barges to the heartland of the United States. Necessity creates opportunities.
Although the role of the FMC had been questioned as part of the “failed experiment,” the commission announced on November 7 that it was engaging with ocean carriers and marine terminal operators to review the process of delivering and returning containers. The present FMC initiative has been referred to as Fact Finding 29, headed by Commissioner Rebecca Dye and begun in March 2020. Its objective was to identify causes of congestion and inefficiencies in the ocean freight intermodal transportation network. The FMC initiative has also been referred to as the International Transportation Supply Chain Engagement, and interim recommendations were issued in July 2021.
The focus has broadly addressed the need to maintain an effective and reliable global freight delivery system as authorized under the 1984 Shipping Act. The FMC initiatives recognized that unresolved supply chain issues existed before COVID-19, and teams were necessary to study ports, terminals, shipping companies, drayage trucking and longshore, rail and chassis providers. Recent small changes such as double moves for trucks improved predictability and addressed the chassis storage shortage issue. The FMC process has created a public-private dialogue that is vital in clarifying processes and addressing problems in a practical manner.
On November 29, the Federal Trade Commission initiated a study to better understand the reasons behind the supply chain disruptions and whether specific issues are leading to “bottlenecks, shortages, [and] anti-competitive practices[,] or contributing to rising consumer prices.”
Crises require solutions but also an opportunity to challenge how we think and handle processes. How does the maritime industry line up the supply chain dominoes and coordinate the intermodal operations to be in sync? What alternatives, such as barge container freight systems and double trucking, among others, exist? How does the maritime industry mine and share data on shipping and delivery to anticipate congestion? The FMC and intermodal transportation industry stakeholders have pulled off the bandage and are addressing the recurring problems accelerated by COVID-19. The current supply chain disruption is not only a crisis but also an opportunity for the public and private sectors to address systemic issues and provide a long-term solution by taking a holistic approach.
Grady S. Hurley is co-leader of the maritime litigation and arbitration team and co-chair of the Energy, Environmental & Natural Resources Industry Team at Jones Walker LLP in New Orleans. In addition to his role at Jones Walker, Hurley is also currently 2nd vice president of the Maritime Law Association. Since 1979, he has focused on maritime, oilfield and energy litigation. You can view his full bio at this link: https://www.joneswalker.com/en/professionals/grady-s-hurley.html