By Ken Kolb, Special to The Waterways Journal
Walter Sons has mastered the art of nearly every shipbuilding skill. From blasting and painting to welding and fitting, he’s done it all. His to-do list each day may have changed since his move into project management years ago, but at his core, he’s a shipbuilder.
As I stood next to him at the Thoma-Sea Shipyard dry dock in Houma, La., Sons pointed to the preparations being made to repair the USS Kidd (DD-661), a famed Fletcher-class destroyer that earned 12 battle stars during World War II and the Korean War. This storied ship is famous for surviving a kamikaze dive bomber attack and more recently serving as the backdrop for the 2020 film “Greyhound” starring Tom Hanks. In need of repairs after years of operation as a naval museum, the Kidd was towed earlier this year all the way from Baton Rouge, La., to be refurbished for its next generation of visitors.
Seeing a historic ship docked at a modern shipyard puts the shipbuilding industry into perspective. Much has changed since the USS Kidd first set sail in 1943. That year marked America’s peak of ship production with 1.4 million Americans employed in the nation’s shipyards. Today, that number has shrunk to 151,000.
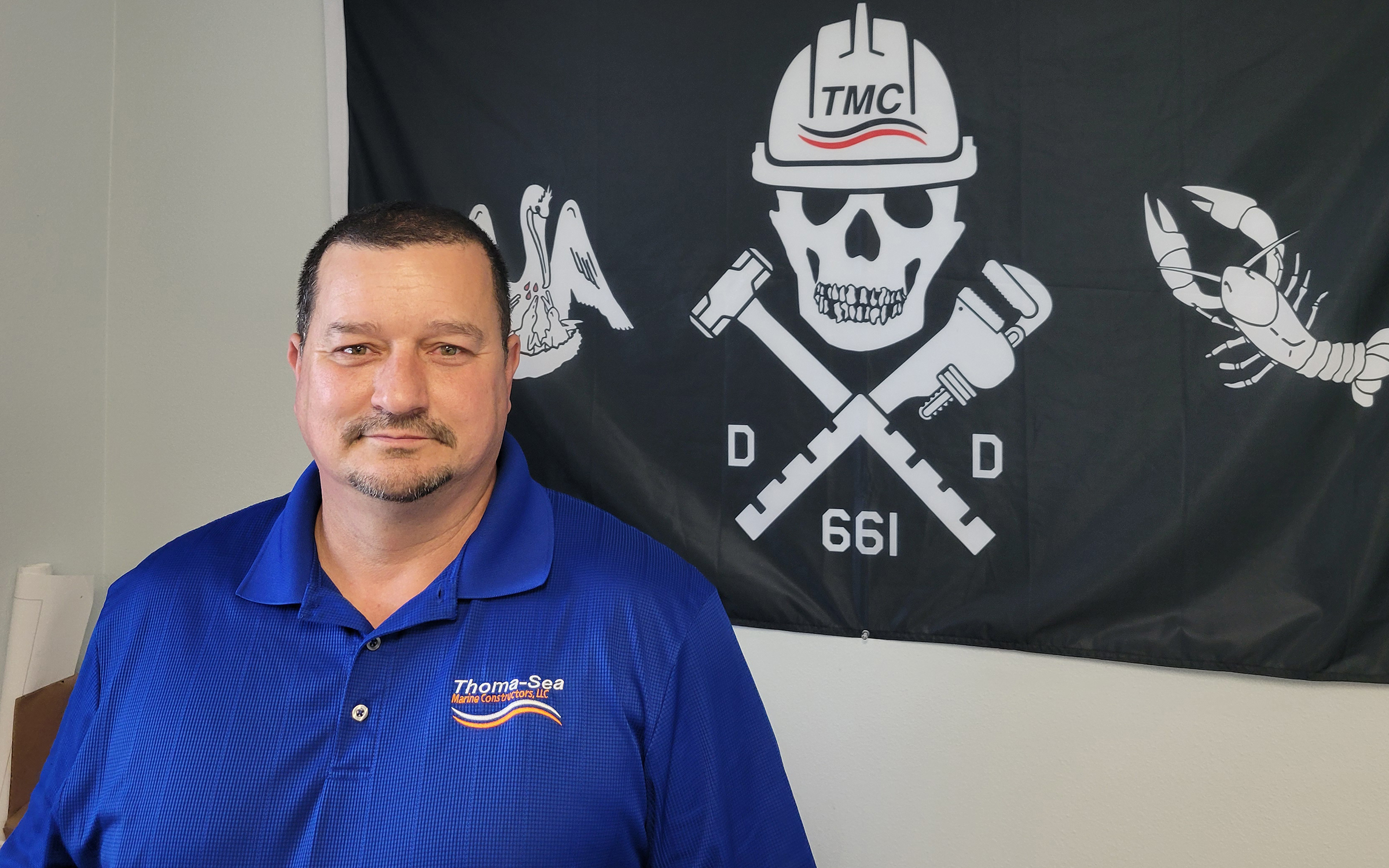
In a way, that number highlights how efficient the process of domestic vessel fabrication has become. At Thoma-Sea, Sons explained to me how the shipyard’s CNC machines can cut through multiple plates of steel at a time to exact specifications, producing stacks of uniform shapes in a matter of days that would have taken weeks or months the year the USS Kidd was constructed. Talking to Sons, I sensed his excitement as he described how fabrication technology has evolved over his career.
On the other hand, though, aside from innovation and automation, the real reason American shipyards employ fewer people today is because the United States is building fewer ships. Starting in the 1980s, with the end of government subsidies, the shipbuilding industry began its steady decline relative to its global competitors. Since 1943, the United States has dropped to 19th place in global ship production. Today, China produces 100 times more large vessels per year than the United States (1,000 ships to our 10).
As I climbed onto the deck of the USS Kidd, Walter Sons described the challenges facing American shipbuilders today. Thoma-Sea does not build cheap, he said, it builds quality. If a buyer wants to spend less, that buyer can find options overseas. The difference in price point is largely driven by raw materials. As an example, Sons pointed to the hull repairs on the USS Kidd. Because this project comes with a “buy American” clause written into its contract, Thoma-Sea will use American steel, as it does on most of its projects.
American steel is more expensive on the front end but is also less prone to carbon pockets and the cracks they produce. At Thoma-Sea, every square inch counts. Even the paint is top shelf. Working with specialists from Sherwin Williams, Sons described how his team discovered the USS Kidd’s exact 1943 color from historical research in the naval archives.
Looking across the yard from the bow of the USS Kidd, I asked if there is any ship Thoma-Sea cannot produce or repair. Sons explained that the only limitation is the depth of the waterways leading into and out of the facility. Besides that, the biggest barrier to increased ship production at Thoma-Sea and other American shipyards is the lack of a nationwide industrial infrastructure to support such large-scale builds, he said.
Take steel, for example. Shipyards in China and South Korea, the world’s top two builders, source more than 85 percent of their steel from their nation’s own mills. In the United States, however, the proportion is flipped. Apart from ships commissioned by the U.S. government, commercial vessels constructed in the United States are made with 85 percent imported steel.
Industries like shipbuilding and steel production are what economists call “mutually generative” in that they sustain and enable each other’s growth. In the decade when the USS Kidd was built, more than 700,000 American’s worked in American steel mills. Since then, through innovation and automation, the United States produces the same amount of steel as the 1940s (80 million metric tons in 2023) with only one-eighth the number of steel workers. Still, our gains in efficiency are not enough to support a competitive shipbuilding sector. Today, China produces 12 times more steel than the United States.
To tap into the full potential of shipyards like Thoma-Sea and move America up the global rankings of shipbuilding will require serious and sustained investment in a self-reliant supply chain of materials, parts, and skilled labor.
The United States already has a capable cadre of blasters, painters, welders and fitters ready to train the next generation and expand their ranks, but growing the shipbuilding sector in the United States will require broader investments in other “mutually generative” industries as well. Shipyards can’t grow in a vacuum. They need a nationwide infrastructure to support their development.
Sometimes it takes a history lesson to get ideas on how to move forward. Looking to the past when the USS Kidd was initially launched might help plot a course for the future of shipbuilding in this country.
About the author: Ken Kolb is a professor and chair of the Department of Sociology at Furman University. He is currently writing a book about shipping on the Lower Mississippi.