Note: The following is sponsored content provided by Main Iron Works.
The September sun was beaming through the skies while the shipbuilders and engineers at the Cenac-owned, Houma-based Main Iron Works were hard at work on the boatbuilder’s most recent project: a new 100′, 6,008-hp Tier 4-compliant ASD tractor tug. New Orleans-based Bisso Towboat Inc. commissioned the vessel in Summer 2018 and celebrated with a fantastic December christening. This new tractor tugboat joins the growing list of boats entering service in compliance with the Tier IV environmental standards established by the U.S. Environmental Protection Agency (EPA). Main Iron Works employed the Selective Catalytic Reduction (SCR) system, able to scrub emissions by converting nitrogen oxide (NOx) into ammonia—otherwise known as urea. During this environmentally-sound process, ammonia is absorbed by ceramic catalyst bricks built directly into the engines. This newfangled system relies on the convergence of the ceramic catalyst and urea dosing and injection processes, simultaneously cutting the amount of NOx, hydrocarbons, and other particulate matter and hydrocarbons released into the environment. As well as greatly reducing the harmful inhalants, SCR systems are proven to be substantially more efficient than Exhaust Gas Recirculation (EGR) systems enacted on older boats. In fact, research demonstrates that SCR systems offer fuel savings of 5-9% versus their older EGR counterparts.
Arlen “Benny” Cenac explained, “This new tug for Bisso will be the most powerful ship-assist tug on the Mississippi River and further establish Bisso’s leading position in the region for the largest fleet of ASD tractor tugs engaged in the Mississippi River ship-assist trade.”
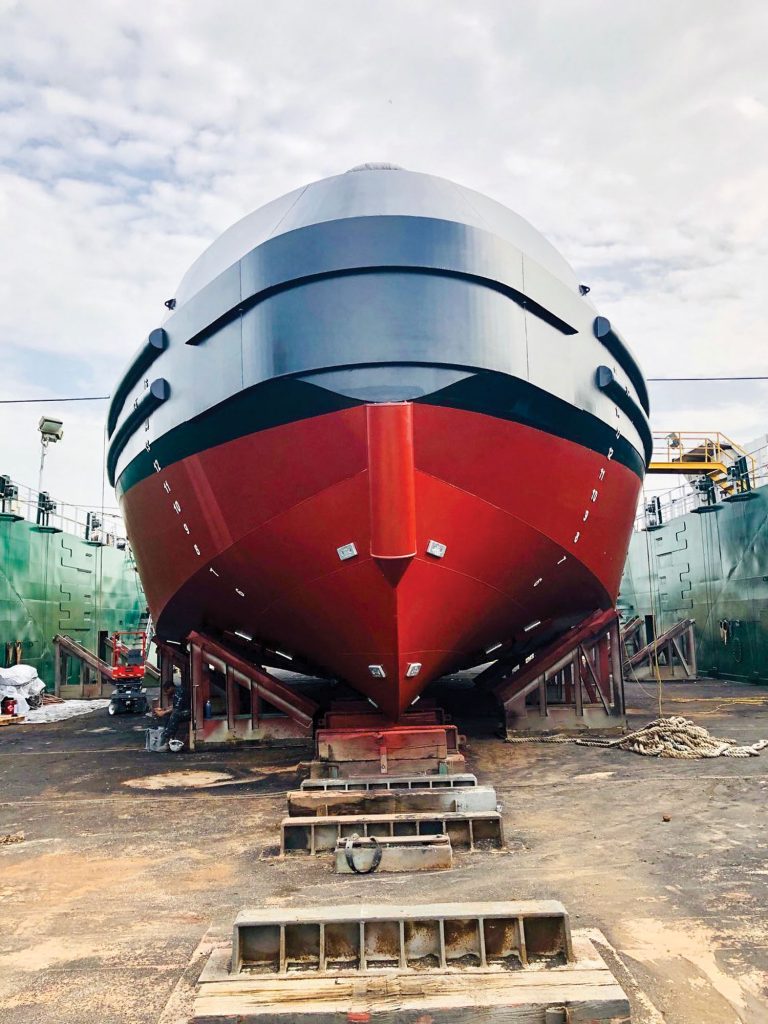
Nearly all of changes between this flagship tow tug and Bisso’s previously commissioned vessels are in the engine room for the SCR system, larger Z-drives, and a larger bow winch and staple to allow for its expanded horsepower and bollard pull. Benny Cenac’s Houma crew utilized Bisso’s existing design with some minor changes in tankage, hull, and other very minor aspects.
The urea tanks were built out of 316 SS and welded into the Port/Starboard ballast tanks of the vessel to hold the ammonia liquid at a stable temperature and balance the vessels tonnage. Since 2010, virtually all new diesel-powered vehicles now come equipped with a urea tank to comply with EPA regulations and remove dangerous pollutants from the exhaust. A dosing unit injects a precise amount—32.5% urea and 67.5% water—of the mixture into the SCR, then, the SCR unit converts that ammonia-laden liquid into exhaust. The heat dispersed by the exhaust allows for the urea to separate into its component parts of carbon dioxide and ammonia, but the catalytic nitrogen converter reacts with the urea and changes it into nitrogen and water—an environmentally innocuous substance that both humans and marine life can tolerate. Top-of-the-line stainless steel piping, air dryers, and air compressors were built to ensure that urea system runs smoothly, introducing the new Bisso tug as one of the most environmentally conscious tractor tugs on the Mississippi River and beyond.
Arlen “Benny” Cenac—Maritime and Conservation Legend Behind Bisso’s New Tug
Arlen “Benny” Cenac, a towing and maritime legend in Houma, is a passionate conservationist intent on preserving the Gulf Coast’s culture and ecology. His professional background and extensive family ties to the maritime industry meshed with his love for the Louisiana bayou—giving way to Cenac’s newest project for Bisso.
The fuel system of the new vessel is situated in the boat’s contained station “box” and remote fuel shutdowns are placed on the outside of the engine room. Now updated from the fire pumps for exterior fire nozzle stations in Bisso’s previous vessels by Main Iron Works, the newly-designed CO2 system suppresses potential fires in the engine and generator rooms, outfitted by eight Herbert Hiller CO2 chambers. Fixed-system water mist and CO2 dry chemical are chosen should an engine room fire erupt, so people can safely breathe in the contained space. Some suppression agents reduce the heat of the fire, but a CO2 fire suppression system eliminates the oxygen needed to sustain a fire. The CO2 level in the space quickly increases, allowing the oxygen levels to drop until the fire is extinguished or reduced. Since CO2 is a colorless, odorless, and electrically non-conductive gas that leaves no residue behind, the ship should be somewhat protected from damages—cutting down on costly repairs or downtime in the fire’s aftermath.
The tug’s main propulsion stems from twin Caterpillar 3516E, Tier 4 diesels, accounting for 3,004 hp at 1,800 rpm each. The twin Caterpillars drive the Rolls-Royce US 255FP azimuthing thrusters with 98.4″x94.3″ 4-bladed stainless-steel propellers in stainless-steel nozzles—affording the new tugboat an outstanding giving the new tug an extremely powerful, 80-ton bollard pull. The auxillary equipment for Bisso’s new tractor tug will include a JonRie 240 escort winch, John Deere 99-kw gensets, and a slew of complimentary safety, monitoring, and electrical equipment all compliant with sub-chapter M regulations. The boat’s capacity allows for 30,162 gallons of diesel fuel; 1,442 gallons of lube oil; 1,442 gallons of hydraulic oil; 3,000 gallons of urea; and 9,538 gallons of potable water. The American Bureau of Shipping (ABS) is the TPI (Third Party Inspector) agency overseeing the Bisso vessel construction, outfitting, and testing. Per usual, all tanks and piping were tested to check for leaks—something Main Iron Works has always performed in-house for each of the vessels built on the premises.